Методика проектирования прямозубых долбяков
После расчета дополнительных параметров зубчатой передачи производится собственно проектирование долбяка, то есть расчет конструктивных и геометрических параметров, определяющих долбяк как геометрическое тело (рис.5.2). В дальнейшем изложении будем полагать, что долбяк проектируется для обработки большего колеса зубчатой передачи (колеса с числом зубьев z2). В случае, если долбяк проектируется для обработки шестерни (меньшего колеса с числом зубьев z1), в последующих формулах следует заменить индекс при переменных «2» на индекс «1». В остальном методика расчета остается неизменной. Полный перечень исходных данных, необходимых для проектирования зуборезного долбяка, представлен в табл. 6.3.
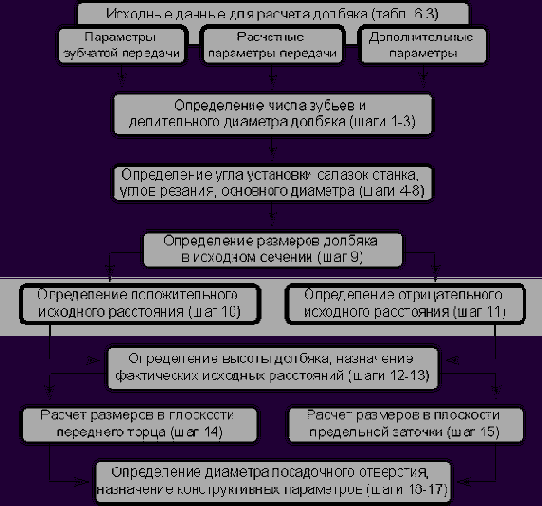
Рис.6.4 Принципиальная схема проектного расчета дискового долбяка
Исходные данные для проектирования дискового зуборезного долбяка
Обозначение параметра | Наименование параметра | Примечания |
Параметры зубчатой передачи, задаваемые чертежом изделия | ||
m | Модуль зубчатой передачи, мм | |
x2 | Коэффициент смещения для обрабатываемого колеса | |
a | Угол профиля исходного контура | |
ha* | Коэффициент высоты головки зуба обрабатываемого колеса | |
hf* | Коэффициент высоты ножки зуба обрабатываемого колеса | Коэффициент высоты ножки зуба может быть определен через коэффициент граничной высоты: hf*=hl*-ha* |
b | Угол наклона зубьев обрабатываемого колеса | Угол наклона зубьев долбяка на делительном цилиндре b0 принимается равным углу наклона зубьев колеса b |
Параметры зубчатой передачи, определяемые расчетом | ||
Dy | Коэффициент уравнительного смещения передачи | Определяется по формуле (6.15), см. С.37 |
d2 | Делительный диаметр обрабатываемого колеса, мм | Определяется по формуле (6.11), см. С.36 |
da2 | Диаметр окружности вершин зубьев обрабатываемого колеса, мм | Определяется по формуле (6.16), см. С.37 |
df2 | Диаметр окружности впадин обрабатываемого колеса, мм | Определяется по формуле (6.17), см. С.37 |
db2 | Диаметр основной окружности обрабатываемого колеса, мм | Определяется по формуле (6.18), см. С.37 |
rp2 | Радиус кривизны в точке начала активной части профиля зуба обрабатываемого колеса, мм | Определяется по формуле (6.20), см. С.38 |
Дополнительные параметры | ||
с0* | Коэффициент радиального зазора в передаче долбяк?колесо | В большинстве случаев расчета может быть принято с0*=0,25 |
j | Боковой зазор в зацеплении, мм | Величина бокового зазора выбирается в зависимости от степени точности передачи по нормам плавности работы. Методика определения величины бокового зазора подробно изложена в [23, с.48-51]. |
Степень точности зубчатой передачи | ||
Модель зубодолбежного станка, на котором будет производиться обработка колес | ||
Модель станка, на котором будет производиться шлифование профиля зубьев долбяка |
1. Первым шагом в проектном расчете долбяка является определение номинального делительного диаметра и числа зубьев инструмента. При выборе делительного диаметра и числа зубьев принимаются в расчет следующие соображения:
а) возможность использования долбяка с выбранным номинальным делительным диаметром на имеющихся моделях зубодолбежных станков. Обычно стремятся на станке заданной модели применять долбяки одного номинального делительного диаметра. Данные о параметрах различных моделей зубодолбежных станков [17, с.93?94] представлены в табл. 6.5;
б) рекомендации ГОСТ 9323–79 в отношении выбора номинального делительного диаметра долбяка. Параметры стандартных долбяков ГОСТ 9323–79 приведены в табл. 5.2 и 5.3 (см. С.27). В табл. 6.4 приведены данные о рекомендованных значениях номинальных делительных диаметров долбяков. При проведении проектного расчета, ориентировочное число зубьев долбяка определяется по формуле

где d0ном – номинальный делительный диаметр долбяка согласно ГОСТ 9323–79, мм. Полученное значение числа зубьев долбяка округляется до целого, желательно четного числа. Целесообразно принимать число зубьев долбяка в интервале от 22 до 40. Такое число зубьев позволяет нарезать зубчатые колеса во всем диапазоне зубьев, обеспечивая практически приемлемые геометрические параметры переходных кривых. Однако, на практике, для долбяков больших модулей, а также для нарезания колес внутреннего зацепления в ряде случаев приходится принимать число зубьев меньше 22. Кроме того, в целях расширения диапазона модулей, охватываемых данным номинальным диаметром, а также для повышения стойкости долбяков проектируются долбяки с числом зубьев больше 40;
в) возможность обработки долбяка на имеющихся моделях зубошлифовальных станков. При изготовлении зубья долбяков шлифуются на зубошлифовальных станках. Поэтому при проектировании долбяка число его зубьев необходимо выбрать таким, чтобы оно было равно или кратно числу зубьев одного из делительных дисков, которые в виде набора прилагаются к зубошлифовальным станкам.
Параметры стандартного набора эвольвентных копиров и делительных дисков к зубошлифовальным станкам приведены в табл. 6.4.
Таблица 6.4
Ряды значений параметров, рекомендованные к использованию при проектировании долбяков
Наименование параметра |
Обозначение параметра |
Рекомендованный ряд значений |
Номинальный диаметр долбяка, мм |
d0ном |
25; 38; 50; 80; 100; 125; 160; 200 |
Число зубьев делительных дисков, прилагаемых к зубодолбежным станкам |
zдиск |
17; 18; 20; 21; 22; 23; 24; 2\5; 27; 28; 29; 30; 31; 32; 34; 36; 37; 38; 40; 41; 42; 43; 44; 45; 46; 47; 48; 51; 52; 53; 54; 58; 60; 61; 62; 63; 64; 66; 67; 68; 70; 72; 73; 74; 75; 76; 78; 80; 83; 88; 90; 100; 102; 103; 115 |
Диаметры основных окружностей эвольвентных копиров |
dbK |
8; 12; 15; 25,4; 26; 34.4; 38.1; 39.4; 45.2; 50; 50.8; 55; 62; 63.5; 70.8; 72; 73,4; 75; 76.2; 88.9; 99; 99.6; 100; 101.6; 103; 107; 125; 142; 150; 162; 164; 171; 178; 180; 198; 202; 225 |
Основные параметры зубодолбежных станков
Завод-изготовитель |
Корсунь-Шевченковский станкостроительный завод (Украина) |
Егорьевский станкостроительный завод (Россия) |
|||
Модель станка |
5111 |
5А122 |
5А122Ф4 |
5А140П |
5А130* |
Наибольший диаметр заготовки |
80 |
250 |
200 |
500 |
250 |
Наибольший модуль нарезаемого колеса |
1 |
6 |
5 |
8 |
10 |
Наибольшая ширина венца |
20 |
50 |
50 |
100 |
105 |
Наибольший делительный диаметр долбяка |
40 |
100 |
100 |
100 |
|
Частота движения долбяка (двойных ходов в мин.) |
26?1600 |
195-1200 |
125-1250 |
55-560 |
40-100 |
Мощность главного привода, кВт |
1,1 |
3 |
11 |
5/6,3/10 |
22 |
Масса станка, т |
1,5 |
5 |
5,4 |
7,5 |
16 |
Завод-изготовитель |
Клинский станкостроительный завод (Россия) |
||||
Модель станка |
5М150П |
5М161 |
51А80ПФ2 |
51А125ПФ2 |
51А200ПФ2 |
Наибольший диаметр заготовки |
800 |
1250 |
800 |
1250 |
2240 |
Наибольший модуль нарезаемого колеса |
12 |
12 |
12 |
12 |
12 |
Наибольшая ширина венца |
160 |
170 |
190 |
190 |
200 |
Наибольший делительный диаметр долбяка |
200 |
200 |
200 |
200 |
200 |
Частота движения долбяка (двойных ходов в мин.) |
33-188 |
33-212 |
30-327 |
30-327 |
5-400 |
Мощность главного привода, кВт |
4,8/5,7/7,5 |
4,8/5,7/7,5 |
10/6,3/5 |
10/6,3/5 |
10 |
Масса станка, т |
9,5 |
10,5 |
11,5 |
11,7 |
18,4 |
Фирма -изготовитель |
Либхер (ФРГ) |
Сейкс (Англия) |
|||
Модель станка |
WS201 |
WS401 |
WS501 |
V1250 |
V400 |
Наибольший диаметр заготовки |
250 |
400 |
500 |
250 |
400 |
Наибольший модуль нарезаемого колеса |
6 |
8 |
8 |
6 |
6 |
Наибольшая ширина венца |
50 |
80 |
140 |
130 |
130 |
Наибольший делительный диаметр долбяка |
186 |
200 |
200 |
100 |
100 |
Частота движения долбяка (двойных ходов в мин.) |
320-2060 |
200-1800 |
31-500 |
50-1000 |
50-1000 |
Масса станка, т |
6 |
7,6 |
8,3 |
3,9 |
Фирма-изготовитель |
Лоренц (ФРГ) |
||||
Модель станка |
SN4 |
SN5 |
SN8 |
SN10 |
LS150 |
Наибольший диаметр заготовки |
210 |
500 |
630 |
1000 |
150 |
Наибольший модуль нарезаемого колеса |
4 |
5 |
8 |
10 |
5 |
Наибольшая ширина венца |
60 |
75 |
180 |
180 |
42 |
Наибольший делительный диаметр долбяка |
100 |
125 |
125 |
200 |
125 |
Частота движения долбяка (двойных ходов в мин.) |
236-900 |
30-424 |
47-300 |
21-175 |
265-1250 |
Масса станка, т |
3,6 |
4,1 |
5,5 |
6 |
5,7 |
2. После выбора числа зубьев долбяка производится определение фактического делительного диаметра долбяка, который рассчитывается по формуле

где z0 – фактическое число зубьев долбяка, выбранное с учетом номинального делительного диаметра и числа зубьев делительного диска зубошлифовального станка.
3. Производится определение теоретического диаметра основной окружности долбяка:

4. Производится определение угла установки салазок зубошлифовального станка. Для равномерного износа шлифовального круга, повышения точности профиля долбяка, достижения большей универсальности в использовании зубошлифовальных станков при шлифовании зубьев долбяка салазки зубошлифовального станка устанавливаются под некоторым углом к оси шлифовального круга, который обозначается aуст. При этом необходимо выдержать условия:


Учитывая сказанное выше, для определения угла установки салазок зубошлифовального станка выполняются следующие действия:
а) определяется диаметр основной окружности эвольвентного копира при условии шлифования зубьев долбяка с углом установки салазок зубошлифовального станка


б) определяется диаметр основной окружности эвольвентного копира при условии шлифования зубьев долбяка с углом установки салазок зубошлифовального станка


в) фактический диаметр основной окружности эвольвентного копира dbК должен находиться в интервале от d¢bK до d²bK и выбирается из ряда диаметров эвольвентных копиров, представленных в табл. 6.4.
г) определяется угол установки салазок зубошлифовального станка:

где dbK – фактический диаметр основной окружности копира зубошлифовального станка. Расчет ведется с точностью до 0,000001, а полученный результат округляется до 1¢ (0,01°).
5. На следующем шаге расчета осуществляется выбор углов резания на вершине зуба долбяка. Как уже отмечалось, наличие положительных передних и задних углов на вершине зуба долбяка ведет к появлению погрешностей нарезаемого колеса. Размеры этих погрешностей зависят от принятых величин передних и задних углов (чем больше эти углы, тем больше погрешности). Поэтому передние и задние углы долбяков выбираются сравнительно небольшими.
Передний угол ga0 для чистовых долбяков принимается равным 5°, а для обдирочных долбяков ga0=10°.
Задний угол на вершине назначается в зависимости от угла главного профиля зуба нарезаемого колеса. Рекомендованные величины заднего угла aа0 приведены в табл. 6.6.
Таблица 6.6
Величина заднего угла на вершине зуба долбяка
Угол главного профиля нарезаемого колеса, a |
Задний угол на вершине долбяка aа0 |
15?17° |
7°30’ |
18?25° |
6° |
26?30° |
4° |
Вследствие совместного влияния на профиль инструмента переднего и заднего углов, профильный угол долбяка будет отличаться от угла профиля нарезаемого колеса:

Расчет ведется с точностью до 0,000001, а полученная величина a0K округляется до 1І (0,0001°).
7. Производится определение расчетных геометрических параметров долбяка на боковых режущих кромках.
а) боковой задний угол в нормальном сечении к боковой режущей кромке определяется по формуле

На угол aбN0 поворачивается шлифовальная головка станка при изготовлении долбяка. Значение aбN0 вносится в рабочий чертеж инструмента. Расчет ведется с точностью до 0,000001, а полученная величина aбN0 округляется до 1І (0,0001°);
б) боковой задний угол на поверхности делительного цилиндра определяется по формуле

Расчет ведется с точностью до 0,000001, а полученная величина aб0 округляется до 1І (0,0001°).
в) передний угол в нормальном сечении к боковой режущей кромке в точке, лежащей на делительном цилиндре определяется по формуле

Расчет ведется с точностью до 0,000001, а полученная величина округляется до 1І (0,0001°).
8. Определение фактического диаметра основной окружности долбяка производится по формуле

9. Определяются размеры долбяка в исходном сечении. Известно, что в исходном сечении долбяк представляет собой зубчатое колесо без смещения, и размеры его точно соответствуют размерам нарезаемого колеса. Поэтому при определении размеров долбяка в исходном сечении используются те же формулы, которые применяются при определении параметров зубчатого колеса, сопряженного в передаче с тем колесом, которое обрабатывается долбяком:
а) толщина зуба долбяка по дуге делительной окружности определяется по формуле

где толщина зуба обрабатываемого колеса по дуге делительной окружности S2 с учетом бокового зазора в передаче определяется по формуле

б) высота головки зуба долбяка принимается равной высоте ножки зуба обрабатываемого колеса:

где высота ножки зуба колеса hf2 рассчитывается по формуле

в) высота ножки зуба долбяка определяется по формуле
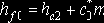
где высота головки зуба обрабатываемого колеса ha2 определяется по формуле

Расчет ведется с точностью до 0,0001, а полученные величины S0, hf0 и ha0 округляются до 0,001;
г) диаметр окружности вершин зубьев долбяка в исходной плоскости определяется по формуле

д) угол давления на вершине зуба долбяка[3] определяется по формуле

е) толщина зуба долбяка на окружности вершин определяется по формуле

10. На шаге 10 производится определение положительного исходного расстояния. Теоретические аспекты определения положительного исходного расстояния изложены в разделе 2 (см. С.11). Положительное исходное расстояние определяется по следующей методике:
а) рассчитывается величина положительного исходного расстояния, при котором гарантируется обработка полной высоты активной части профилей зубьев колеса. В первую очередь определяется станочный угол зацепления нового (индекс «Н») долбяка, обеспечивающий полную обработку рабочей части профиля зуба колеса по формуле

Расчет ведется с точностью до 0,000001, а полученная величина a¢wН округляется до 1І (0,0001°).
Положительное исходное расстояние, обеспечивающее полную обработку рабочей части профиля зуба колеса рассчитывается по формуле

б) положительное исходное расстояние, лимитируемое заострением зубьев долбяка, определяется по формуле

где Sa0min – минимально допустимая длина периферийной (вершинной) режущей кромки.
Минимальная длина периферийной режущей кромки определяется по формуле

в) из двух полученных значений a¢Н и a²Н для дальнейших расчетов принимают меньшее, которое обозначают символом aН.
11. Производится определение отрицательного исходного расстояния. Как указывалось выше (см. раздел 2, с.11), отрицательным исходным расстоянием называется расстояние от исходного сечения до торцевого сечения предельно сточенного долбяка. При проектировании долбяка определяется максимальная величина отрицательного исходного расстояния, при которой обеспечивается выполнение трех условий: условия отсутствия срезания головки зуба колеса; условие полной обработки зубьев, условие отсутствия подрезания ножки зуба колеса:
а) производится определение отрицательного исходного расстояния, при котором гарантируется отсутствие среза на головках зубьев колес или неполной обработки головок зубьев. Для этого определяется станочный угол зацепления предельно сточенного долбяка, гарантирующий отсутствие среза на головках зубьев колес или неполной обработки головок зубьев по формуле

где r2max - наибольший радиус кривизны профиля зуба нарезаемого колеса:

r0 ? минимальный радиус кривизны профиля зуба долбяка. Величина минимального радиуса кривизны профиля зуба долбяка определяется в зависимости от номинального диаметра d0:
d0 r0
Менее 75 мм.......................... 2 мм
75?99 мм........................... 3 мм
100 мм и более........................ 5 мм
Расчет ведется с точностью до 0,000001, а полученная величина a¢wC округляется до 1І (0,0001°).
Отрицательное исходное расстояние, при котором отсутствует срез на головках зубьев колес или неполная обработка головок зубьев выполняются по формуле

б) определение отрицательного исходного расстояния из условия отсутствия подрезания ножки зуба нарезаемого колеса производится только в том случае, когда диаметр окружности впадин обрабатываемого колеса меньше диаметра основной окружности этого колеса, то есть имеет место неравенство

При этом определяется станочный угол зацепления, при котором происходит начало подрезания ножки зуба обрабатываемого колеса по формуле

Расчет ведется с точностью до 0,000001, а полученная величина a²wC округляется до 1І (0,0001°).
Отрицательное исходное расстояние предельно сточенного долбяка, при котором будет происходить начало подрезания ножек зубьев нарезаемых колес, определяются по формуле

в) из двух полученных значений a¢C и a²C для дальнейших вычислений выбирается одно, которое обозначается aC. Величины a¢C и a²C могут иметь разные знаки или обе быть отрицательными. В случае наличия разных знаков за расчетные значения AC следует принять положительную величину и плоскость окончательной переточки долбяка расположить правее исходного сечения I?I (рис. 6.5, б). При отрицательных значениях a¢C и a²C за расчетную величину необходимо принять меньшее по абсолютной величине и плоскость окончательной переточки долбяка расположить левее исходного сечения I?I (рис. 6.5, а).
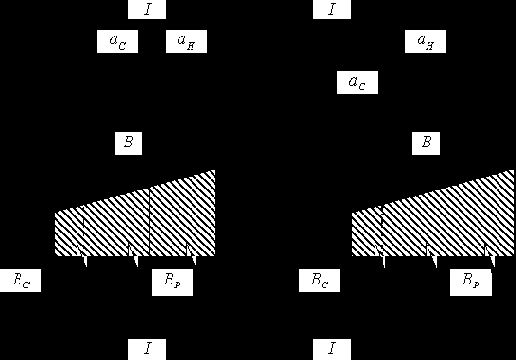
а б
Рис.6.5 Схема к определению расчетных значений исходных расстояний
12. Производится определение высоты долбяка. Высота долбяка определяется как сумма высоты рабочей части долбяка и высоты окончательно сточенного долбяка (рис. 6.5).

где BP – высота рабочей части долбяка; BС – высота окончательно сточенного долбяка. Высота окончательно сточенного долбяка берется из табл. 6.7. Высота рабочей части долбяка чаще всего определяется расчетными значениями исходных расстояний.
Так, по рис. 6.5, а высота рабочей части

а по рис. 6.5, б

Однако, помимо исходных расстояний, высота долбяка может лимитироваться технологическими требованиями шлифования профиля зубьев долбяка. При шлифовании зубьев долбяка отсутствует продольная подача круга относительно долбяка. В результате этого впадина зуба получается вогнутой, что может привести к ослаблению или подрезу зубьев долбяка (рис. 6.6). Эти ограничения не относятся к категории расчетных и задаются в виде таблицы максимальных высот долбяка, составленной на основе практического опыта. Рекомендуемые высоты рабочей части долбяка, допустимые технологическими требованиями, приведены в табл. 6.7.
Таблица 6.7
Рекомендуемые величины высот долбяка, мм
Модуль m |
Номинальный делительный диаметр ![]() |
Максимальная высота рабочей части долбяка ![]() |
Высота полностью изношенного долбяка ![]() |
1,00–1,50 |
80 |
18 |
4 |
1,75–2,50 |
80 |
20 |
5 |
2,75–5,00 |
80 |
21,5 |
6,5 |
1,00–1,50 |
100 |
19 |
4 |
1,75–2,50 |
100 |
23,5 |
4,5 |
2,75–4,00 |
100 |
28,5 |
5,5 |
4,50–5,00 |
100 |
29,5 |
6,5 |
5,50–8,00 |
100 |
32,5 |
7,5 |
![]() Рис.6.6 Форма ножки зуба после шлифования профиля зубьев |

где

13. На шаге 13 производится назначение фактических величин положительного и отрицательного исходных расстояний долбяка:
а) в том случае, если выполняется условие

(то есть в тех случаях, когда сумма расчетных значений положительного исходного расстояния и абсолютной величины отрицательного исходного расстояния не превышает допустимой высоты рабочей части долбяка, рис. 6.7, а), фактические величины положительного и отрицательного исходных расстояний принимаются равными их расчетным значениям, то есть


б) если сумма исходных значений положительного исходного расстояния и абсолютной величины отрицательного исходного расстояния больше максимально допустимой технологическими требованиями высоты рабочей части долбяка, то есть если имеет место неравенство

исходное расстояние долбяка располагают по одному из трех вариантов: симметрично относительно рабочей высоты долбяка, с полным использованием положительного исходного расстояния или с полным использованием отрицательного исходного расстояния, после чего производят корректировку величин исходных расстояний. Выбор того или иного варианта расположения исходных расстояний зависит от конкретных условий.
При проектировании долбяков средних модулей (m=1...5 мм), а также крупномодульных с m>5 мм и числом зубьев z0>15 принимается симметричное расположение исходного сечения (рис. 6.7, б). В этом случае фактические исходные расстояния определяются следующим образом:
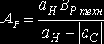
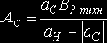
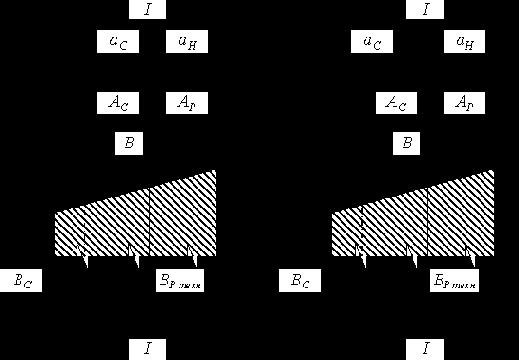
а б
Рис.6.7 Расположение исходного сечения долбяка: с полным использованием положительного и отрицательного исходного расстояния (а) и симметричное (б)
При проектировании крупномодульных долбяков (m>5 мм) с малым числом зубьев (z0<15) исходное сечение располагают с полным использованием положительного исходного расстояния (рис. 6.8, а), а фактические исходные расстояния определяют по формулам


При проектировании долбяков под шевингование, а также мелкомодульных (m<1 мм) долбяков, исходное сечение долбяка располагают с полным использованием отрицательного исходного расстояния (рис. 6.8, б), а фактические исходные расстояния определяют по формулам


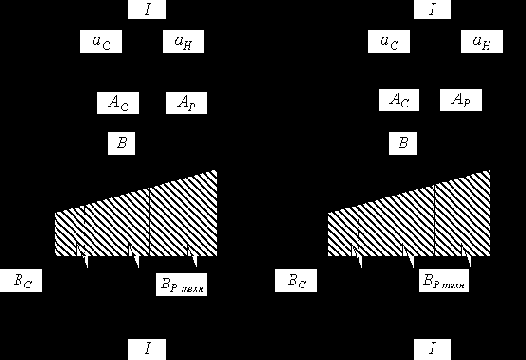
а б
Рис.6.8 Расположение исходного сечения долбяка с полным использованием положительного (а) и отрицательного (б) исходного расстояния
14. Определение размеров долбяка в плоскости его переднего торца.
В плоскости переднего торца, или, как часто говорят, в режущей плоскости, долбяк, чаще всего, представляет собой зубчатое колесо с положительным смещением исходного контура, и размеры его определяются как размеры обычного зубчатого колеса с положительным смещением. При этом выполняются следующие расчеты:
а) величина смещения исходного контура инструментальной рейки в режущей плоскости определяется по формуле

где aа0 - задний угол на вершине зуба долбяка;
б) толщина зуба долбяка по дуге делительной окружности определяется по формуле

где S0 - толщина зуба долбяка по дуге делительной окружности в исходном сечении;
в) определяется высота головки зуба долбяка в режущей плоскости. При этом используется формула:

г) определяется высота ножки зуба долбяка в режущей плоскости. Вычисление производится по формуле

д) определяется диаметр окружности вершин зубьев долбяка:

е) диаметр окружности впадин зубьев долбяка рассчитывается по формуле

Расчет по всем формулам, приведенным в п.14, производится с точностью до 0,0001 мм.
15. Определение размеров долбяка в плоскости предельной заточки.
В плоскости предельной заточки долбяк чаще всего представляет собой зубчатое колесо с отрицательным смещением исходного контура, и размеры его определяются как размеры обычного зубчатого колеса с отрицательным смещением исходного контура.
При определении размеров долбяка в плоскости предельной заточки величину отрицательного исходного расстояния следует брать с учетом его знака (то есть считать отрицательным). Вычисления производятся в следующей последовательности:
а) величина смещения исходного контура инструментальной рейки в плоскости предельной заточки определяется по формуле

б) толщина зуба долбяка по дуге делительной окружности определяется по формуле

в) высота головки зуба долбяка в плоскости предельной заточки определяется по формуле

г) высота ножки зуба долбяка в плоскости предельной заточки определяется по формуле

д) диаметр окружности вершин зубьев долбяка в плоскости предельной заточки определяется по формуле

е) диаметр окружности впадин зубьев долбяка в плоскости предельной заточки вычисляется по формуле

Расчет по всем формулам, приведенным в п.15, производится с точностью до 0,0001 мм.
16. Определение диаметра посадочного отверстия d1.
Диаметр посадочного отверстия долбяка выбирается по данным табл. 5.3 (см. С.28) и табл. 6.5 (см. С.47) в зависимости от модели зубодолбежного станка, на котором будет применяться проектируемый долбяк.
17. На шаге 17 производится назначение остальных конструктивных параметров долбяка (см. рис. 5.2, с.28). Выбираются значения следующих конструктивных параметров инструмента:
а) диаметра выточки d2;
б) диаметра опорной поверхности d3;
б) ширины ступицы b1.
Назначение величин размеров производится конструктивно с учетом соответствующих размеров стандартных дисков долбяков.
Проведенный расчет полностью определяет геометрию дискового долбяка для обработки прямозубых зубчатых колес и достаточен для назначения технических требований на инструмент (см. раздел 7, с.67) и выполнения его рабочего чертежа.